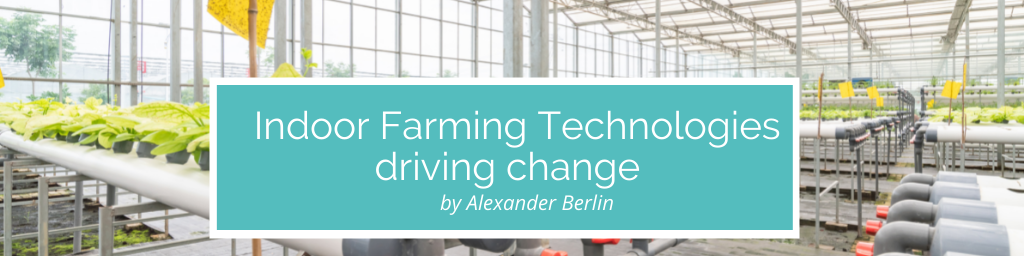
By Alexander Berlin, Berlin Thinking Consulting
In the 4-year experience of IoF2020, we could successfully measure and prove the impact of digital transformation to make our food supply chain more sustainable, fair, efficient, and resilient. Part of this endeavour in IoF2020 focused on vertical farming together with Signify and showed the huge potential of indoor farming in regards of efficient input usage, food quality and shorter supply chains. Now indoor food production technologies are booming, and it is not just vertical farming, even bigger will be the impact of food production in bioreactors. Technologies like precision fermentation for milk products, cell-cultivation for meat and biomass fermentation for alternative proteins such as mushrooms.
Indoor farming technologies are on the verge world-wide with large scale investments in vertical farming like in France with €42M for Jungle, €8.5M for Nordic Harvest in Denmark or €170M for Infarm in Germany, but also with novel food producer such as German precision fermentation startup Formo with €50M investment or €85M for the Dutch cultivated meat company Mosa Meat. The sustainable production of high-quality food is a key challenge for many countries in world of climate change, world population growth and dangerous dependencies on imports for countries with low agricultural production. Indoor farming is independent from any climate conditions, its highly efficient in terms of nutrition and water use, secure from any pests, diseases or other pathogens and it allows production throughout the whole year. However, there is still a significant downturn which is the energy consumption for the heating and lighting of indoor farming facilities as well as the high investment costs into the equipment. Many novel food technologies in the field of fermentation and cell-cultivation rely furthermore on expensive nutrient solution. All these components keep the price per unit still rather high and hardly competitive with the conventional farming.
The challenge for our European agrifood innovation ecosystem is now to support our startups in making their technologies more efficient by means of technical innovation, circular synergies and interoperable integrations into smart cities and supply chains. Germany is making a step in this direction by building dedicated digital innovation hubs in Germany for the further development of indoor farming technologies especially looking into circular production processes. Currently 2 locations in Germany are in its development with the Food Campus in Berlin and the Future Food Campus in Hamburg. The vision is that these facilities offer the necessary infrastructure like vertical farming modules, bioreactors, cleaning rooms and food labs to accelerate the product development and push European startups to the top indoor farming companies in the future. The locations will be synergistically working together embedded in the European network of Digital Innovation Hubs and food innovation networks such as EIT Food. Here are the 2 emerging locations that will support urban farming technologies in a short overview:
One of the key innovation services that the Future Food Campus in Hamburg envision is an AI-driven process simulation tool that calculates the most efficient and synergetic combination of urban food production technologies based on their digital twins. Therefore, they aim to create digital twins covering several indoor farming modules and novel food production technologies from vertical farming and aquaponics over precision fermentation and cell cultures to algae production. The focus is mainly on the necessary input and output of resources like water, nutrition, energy, heat, light, etc. and its chronological appearance in the growth process. In a second step they plan to work with an expert company on the AI-driven simulation to gain insights on potential synergies between modules that reduces the need for resources. A special focus is here one the energy efficiency of a synergetic and circular combination of modules. Another aspect is the visualization of the data in form of virtual reality simulations, which can help in the design process of future food factories.
Let’s summarize. It needs physical testing and experimentation facilities for our entrepreneurial innovators to develop their technologies in quicker pace and in an open collaborative environment with other companies. Interoperability, data exchange, security, retro fitting and integratability should be key principles for the development of these future solutions. This way we can implement them quickly into our existing infrastructures and they can help in the coming decade to transform our food production towards higher sustainability, free agricultural land for renaturalization and increased biodiversity as well as a lower CO2 footprint by short supply chains.
Author: Alexander Berlin is a future food evangelist and innovation network orchestrator with professional expertise in data-driven business models, digital technologies and innovation funding on the European level. As CEO and Founder of Berlin Thinking Consulting, he provides acceleration and transformation services for tech startups and larger corporates pushing for digitizing their business models through IoT technology. Recently he led the business support of the €35M EU project IoF2020 and is now supporting digital innovations hubs like the food campuses in Germany.